In recent years, driven by the “dual carbon” strategic goal, lightweight materials have been further developed and applied. Since the local mass production of the second-generation aluminum-silicon coated hot-formed steel Uisbor 2000 and Ductibor 1000 in 2019, the application proportion of many new models has increased year by year in just a few years. How do these two materials stand out among many lightweight materials and become the new “group pet”?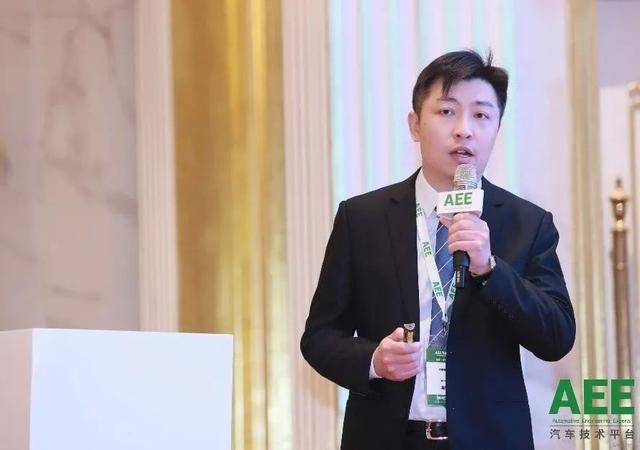
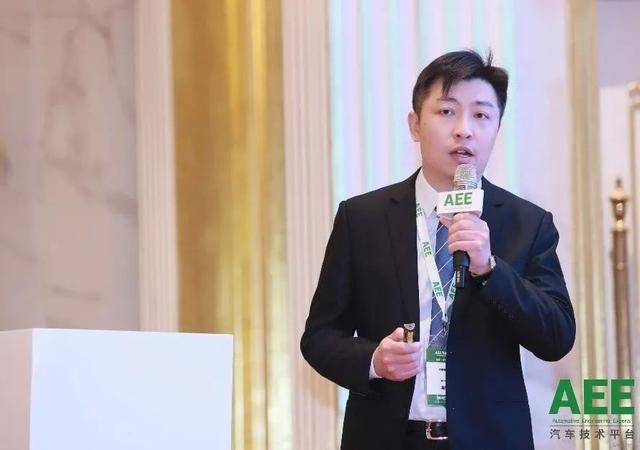
Feb. 22, Hefei, China. VAMA Customer Technical Support Minister Yang Zheng shared the latest hot forming technology and lightweight application results in the industry with many automotive manufacturing experts at the AEE2023 Automotive Technology Annual Meeting, with the theme of “Introduction of the second generation of aluminum silicon coated hot forming steel products and applications”.
Thanks to its ultra-high strength, excellent mechanical properties and simple hot forming production process, aluminum-silicon coated hot forming steel is particularly suitable for lightweight body structural parts and reinforcement parts.
Compared with other hot-formed boron steels, especially bare plates, the production of aluminum-silicon coated hot-formed steel does not need to add any protective gas in the heating furnace, the surface of the hot-formed parts will not form oxide and decarburization, eliminating the subsequent shot blasting process, especially suitable for high temperature hot stamping process. The new generation of Uisbor 2000 and Ductibor 1000 further enhance the performance of the material, especially in the lightweight and safety performance of the body. At the same time, it can also match the existing mature hot stamping process and production line, and realize the new product switch more quickly.
The higher the strength of conventional steel, the worse the formability. The hot-formed steel skillfully avoids this contradiction with the help of the hot-stamping process. The strength and toughness of the second generation aluminum-silicon coated hot-formed steel can achieve a perfect balance under the special chemical composition system and microstructure. Usibor 2000 is used in the hard zone with a strength of up to 2000MPa, which is difficult to achieve with other lightweight materials; Ductibor 1000 is used in soft areas, while retaining enough material toughness, the strength of the first generation material Ductibor 500 increased by twice. The use of Usibor 2000 and Ductibor 1000 for passive safety structures results in a further weight reduction of more than 10% compared to the previous generation portfolio. With the rapid development of new energy vehicles, the lightweight potential and energy saving and emission reduction advantages of the second-generation aluminum-silicon coated hot-formed steel have become more prominent.
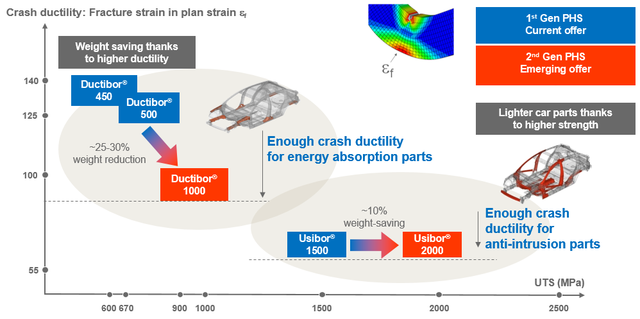
In addition to the development of new steel grade, VAMA, based on its thermoformed steel portfolio, together with GONVVAMA, has innovatively proposed a multi-part integration (MPI) solution to address the multiple challenges of automotive electrification transformation.
Taking H beam as an example, based on the application of the second-generation aluminum-silicon coated hot-formed steel and MPI integration program, the rear longitudinal beam, connecting rod and other structural parts of the lower body are connected together in one stamping process, which greatly saves the intermediate processing link of the lower body and achieves more than 10% weight reduction effect.
With a focus on improving body weight, safety performance and cost effectiveness, the design of automotive components will be further integrated, and VAMA advanced high-strength steels, especially aluminum-silicon coated thermoformed steels, and innovative manufacturing processes will be more widely used in the production of electric vehicle transformation, leading the automotive industry to a more sustainable future.
Thermoformed steel is the promoter of electric transformation of automobile
In recent years, driven by the “dual carbon” strategic goal, lightweight materials have been further developed and applied. Since the local mass production of the second-generation aluminum-silicon coated hot-formed steel Uisbor 2000 and Ductibor 1000 in 2019, the application proportion of many new models has increased year by year in just a few years. How do these two materials stand out among many lightweight materials and become the new “group pet”?
Feb. 22, Hefei, China. VAMA Customer Technical Support Minister Yang Zheng shared the latest hot forming technology and lightweight application results in the industry with many automotive manufacturing experts at the AEE2023 Automotive Technology Annual Meeting, with the theme of “Introduction of the second generation of aluminum silicon coated hot forming steel products and applications”.
Thanks to its ultra-high strength, excellent mechanical properties and simple hot forming production process, aluminum-silicon coated hot forming steel is particularly suitable for lightweight body structural parts and reinforcement parts.
Compared with other hot-formed boron steels, especially bare plates, the production of aluminum-silicon coated hot-formed steel does not need to add any protective gas in the heating furnace, the surface of the hot-formed parts will not form oxide and decarburization, eliminating the subsequent shot blasting process, especially suitable for high temperature hot stamping process. The new generation of Uisbor 2000 and Ductibor 1000 further enhance the performance of the material, especially in the lightweight and safety performance of the body. At the same time, it can also match the existing mature hot stamping process and production line, and realize the new product switch more quickly.
The higher the strength of conventional steel, the worse the formability. The hot-formed steel skillfully avoids this contradiction with the help of the hot-stamping process. The strength and toughness of the second generation aluminum-silicon coated hot-formed steel can achieve a perfect balance under the special chemical composition system and microstructure. Usibor 2000 is used in the hard zone with a strength of up to 2000MPa, which is difficult to achieve with other lightweight materials; Ductibor 1000 is used in soft areas, while retaining enough material toughness, the strength of the first generation material Ductibor 500 increased by twice. The use of Usibor 2000 and Ductibor 1000 for passive safety structures results in a further weight reduction of more than 10% compared to the previous generation portfolio. With the rapid development of new energy vehicles, the lightweight potential and energy saving and emission reduction advantages of the second-generation aluminum-silicon coated hot-formed steel have become more prominent.
In addition to the development of new steel grade, VAMA, based on its thermoformed steel portfolio, together with GONVVAMA, has innovatively proposed a multi-part integration (MPI) solution to address the multiple challenges of automotive electrification transformation.
Taking H beam as an example, based on the application of the second-generation aluminum-silicon coated hot-formed steel and MPI integration program, the rear longitudinal beam, connecting rod and other structural parts of the lower body are connected together in one stamping process, which greatly saves the intermediate processing link of the lower body and achieves more than 10% weight reduction effect.
With a focus on improving body weight, safety performance and cost effectiveness, the design of automotive components will be further integrated, and VAMA advanced high-strength steels, especially aluminum-silicon coated thermoformed steels, and innovative manufacturing processes will be more widely used in the production of electric vehicle transformation, leading the automotive industry to a more sustainable future.